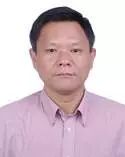
杜泽学,教授级高级工程师,中国石化新能源研究所副所长,主要从事石油化工和新能源相关催化材料和工艺研究开发。作为课题负责人,先后主持国家重点基础研究发展计划(973计划)、国家高技术研究发展计划(863计划)、国家重点研发计划和中国石化开发项目40余项,发表论文70余篇,申请发明专利150多件,其中授权100多件,出版专著和译著2本。2013年荣获首届闵恩泽能源化工奖杰出贡献奖,2015年和2018年分别获得中国石化前瞻性三等奖(2015年)和技术发明二等奖(2018年)。
生物柴油是以生物质为原料生产的、与化石柴油性质相似、可以替代化石柴油的可再生液体生物燃料。油脂是制备生物柴油的主要原料。天然油脂中的长链脂肪酸既可以与低碳醇反应制备脂肪酸酯类生物柴油(即第一代生物柴油),也可以通过加氢反应制备烃类生物柴油(即第二代生物柴油);除油脂外,其他生物质气化后,经过F-T反应也可合成汽油、煤油、柴油等多种燃料。
生物柴油燃烧时排放的二氧化碳来源于生物质生长过程中所固定的二氧化碳,所以使用生物柴油不仅可以减少化石能源的消耗,还可以显著降低温室气体排放。研究还表明,化石柴油与脂肪酸酯类生物柴油混合使用后,可以显著改善发动机尾气排放,如减少颗粒物、烃类物质和CO排放,降低排放气体中的多环芳烃等。脂肪酸酯类生物柴油含有酯基及其他极性基团,所以具有较好的润滑性能,向化石柴油中加入少量脂肪酸酯类生物柴油可以显著改善化石柴油的润滑性能,这是低成本解决低硫柴油润滑性不足的可选方案。此外,由于脂肪酸酯类生物柴油的分子结构中还保留有长链脂肪酸基团,所以它还可以作为油脂化工的原料,生产各种油脂化学品。由于脂肪酸酯类生物柴油具有上述诸多优点,目前人们提及“生物柴油”时一般是指脂肪酸酯类生物柴油。因甲醇是价格最低的低碳醇,所以最常见的生物柴油是脂肪酸甲酯。
依据使用的催化剂不同,脂肪酸酯类生物柴油的生产工艺可以分为碱催化工艺、酸催化工艺、酶催化工艺以及不使用催化剂的超临界流体反应工艺。碱性催化剂催化三甘油酯与低碳醇发生酯交换反应速度快,原料转化率高,反应条件也比较温和,但碱性催化剂会与原料油中的脂肪酸发生皂化反应,严重影响反应物和产物分离,所以该工艺对原料的酸值和水分有严格限制。欧美国家以优质油脂为原料生产生物柴油时,多采用碱催化工艺,例如鲁奇工艺、Esterfip-H固体碱工艺等。酸性催化剂可同时催化低碳醇与甘油酯或脂肪酸的酯交换反应和酯化反应,所以酸催化工艺对原料油的要求低,而且常用的硫酸、磺酸等催化剂价格十分便宜,所以国内酸化油、地沟油等劣质原料油多采用该工艺生产生物柴油。不过,酸催化工艺反应速率较慢,原料油的转化率也比较低,酸性催化剂对设备和管线还存在一定的腐蚀,生产过程中排放的废水严重污染环境,环保部门对该工艺的限制将越来越高。酶催化剂具有选择性高、反应条件温和等优点,催化剂也多具有对酯化和酯交换双重催化活性,所以该工艺对原料油的要求比较低,但酶催化剂价格昂贵,使用过程中易中毒或失活,限制了该工艺的广泛应用。超临界反应工艺不使用催化剂,无严重腐蚀和三废排放等问题,对原料适应性好,反应后的产物分离也相对简单,所以研究者、开发者众多。本文简要介绍超临界流体反应工艺制备生物柴油的进展及应用前景。
1 超临界流体技术用于生物柴油
制备的理论基础
1.1 超临界流体技术简介
超临界状态(supercritical state, SC)是Thomson在1869年首次观察到的特殊物质存在状态。当流体温度和压力同时高于临界温度(Tc)和临界压力(Pc)时,气液相界线消失,此时的流体即为超临界流体(supercritical fluid,SCF)。温度高于240℃、压力高于7.86MPa的区域即为超临界甲醇区域。
超临界流体兼具液体和气体两种流体的优点,黏度小、扩散系数大,具有极好的溶解特性和传质特性,这使得超临界流体技术在分离、反应、分析等诸多应用领域都显示出极佳的应用效果。近30年来,随着工业制造水平的提高,越来越多的超临界流体技术(supercritical fluid technology,SFT)走向实用化和工业化,成为绿色加工技术的典范。
在临界点附近,超临界流体压力和温度的微小变化都可能导致密度的巨大变化,而流体的黏度、介电常数、扩散系数和溶解能力等性质都与密度关系密切,因而可以方便地通过调节温度和压力来控制超临界流体的物理化学性质。
1.2 超临界流体技术用于
生物柴油生产的基础
超临界状态对化学反应的影响主要包括:压力变化影响反应速率常数;流体扩散系数比液体的大,而密度却比液体小,更具有气体的特征;超临界条件能增加反应物的溶解度,减少传质阻力;超临界流体溶剂分子包围在溶质分子周围,使局部密度显著高于本体密度。
无催化剂条件下,超临界甲醇与油脂反应是通过甲醇在高温条件下的解离作用和质子化作用,分别形成甲氧基离子和质子化甲醇,并与甘油三酸酯分子上的酰基发生碰撞来实现的。
Kusdiana等认为,非超临界条件下,甲醇羟基中的氧与氢之间存在较强的氢键相互作用,甲醇以簇的形式存在,但在超临界状态下,由于温度升高氢键被削弱,甲醇的极性减弱而疏水性增强,介电常数变低,这就增强了甲醇对甘油三酸酯的溶解能力,进而改善传质。商紫阳等计算大豆油与甲醇之间的溶解度参数,发现在260~350℃数值非常接近,说明在该条件下,大量油脂溶解于甲醇中,使酯交换反应接近于在拟均相进行。
超临界状态的高温条件除促进甲醇解离、改善甲醇对油脂的溶解度外,还增加了活化反应物分子的百分数,这也是在超临界条件下不使用催化剂、反应也能快速进行的重要原因。
2 超临界流体技术制备生物柴油研究进展
典型超临界反应制备生物柴油的工艺条件是350℃、45MPa、醇油摩尔比42∶1,菜籽油在此条件下与甲醇反应240s就可以获得95%的甲酯收率。与之形成鲜明对比的是,大豆油与甲醇在150℃、醇油摩尔比6∶1的条件下反应4h也只能获得0.03%的甲酯收率。对比甲酯生成速率,超临界反应制备生物柴油的优势极其显著,所以在2000年左右超临界流体技术成功应用于生物柴油制备后,学术界和产业界都开展了诸多相关研究,下面简要介绍超临界流体制备生物柴油技术的研究进展。
2.1 反应温度
反应温度是影响超临界流体技术制备生物柴油的最关键因素,其对反应的影响主要体现在如下几个方面 :促进甲醇解离,产生更多活性态基团;提高油脂与甲醇的相互溶解度,改善传质。
Demirbas研究不同反应温度下甲酯收率随时间的变化,发现在177~250℃反应温度区间内,相同反应时间的甲酯收率随温度升高不断提高,说明提高温度有利于加快反应速率。他们还发现,240℃与250℃的甲酯生成速率较为接近,但与230℃和220℃的甲酯生成速率存在显著差异,这说明临界点附近反应体系发生了明显变化。
Kusdiana等研究菜籽油与甲醇在近/超临界条件下的反应时发现,反应温度在200~230℃时,反应速率较慢,反应1h甲酯收率仅为68%~70% ;反应温度提高到270℃时,反应体系的压力达到14MPa,尽管此时反应体系的温度和压力都高于甲醇的临界点,传质限制已经大为减弱,但酯交换反应的速率依然不高;只有当反应温度提高到300℃以上时,反应速率才会显著升高,反应240s后脂肪酸甲酯的收率才能达到80%~95%。商紫阳等比较豆油与甲醇在220~350℃甲酯生成速率的差异,也发现260℃以下甲酯生成速率显著低于300℃。反应温度为260℃时,反应体系已经处于超临界状态,油脂与甲醇也形成了均一相,反应速度却不快,所以他们提出超临界流体促进油脂与甲醇溶解并不是超临界酯交换反应能迅速完成的唯一解释,反应活化能也是关键。
He等计算了28MPa、醇油摩尔比42∶1 时,大豆油和多种甘油三酸酯纯物质与甲醇反应的表观活化能,结果表明,反应温度从210~230℃的低温升至240~280℃的高温时,大豆油的表观活化能从11.2kJ·mol-1升至56.0kJ·mol-1, 各甘油三酸酯纯物质的表观活化能则从8.93~16.2kJ·mol-1升至39.0~74.7kJ·mol-1,不同甘油三酸酯纯物质的表观活化能增幅差异较大。
尽管高温有利于提高反应速度,也要防止高温导致油脂原料和脂肪酸甲酯产品的热分解。棕榈油的热重分析结果表明,在氮气氛围下,棕榈油在278.8℃时可以观察到0.97%的失重,即棕榈油开始发生热分解;温度升至381℃时,失重速率达到极大值。进一步分析超临界反应过程中脂酸甲酯的稳定性发现,多不饱和脂肪酸甲酯在270℃、17MPa之前不会发生热分解,从300℃、26MPa后开始发生热分解,而且分解速率随着温度的升高而加快;饱和脂肪酸甲酯则在350℃、43MPa下才开始发生分解。Marulanda 等分析了鸡脂在400℃、20MPa条件下超临界反应8min后的分解产物,主要是短碳链脂肪酸酯和烃。
2.2 反应压力
在超临界条件下,油脂与低碳醇互溶,已经形成均相反应,体系压力进一步增加会继续提高单位体积内反应底物的浓度,加快反应速度。
商紫阳等计算了油脂和甲醇的溶解度参数,结果表明两者的溶解度参数差值随体系压力增加而减小,这说明表明油脂在甲醇相中的溶解度随压力升高而增加。
Song等在350℃、醇油摩尔比为60∶1的条件下,研究反应压力对精制棕榈油超临界反应的影响,结果发现反应压力为5MPa时,未达到超临界状态,反应40min后产物中的甲酯含量不到5% ;提高反应压力,产物中甲酯含量不断升高,至30MPa时甲酯含量达到90%左右,继续升高反应压力到45MPa,甲酯含量不再变化。
Biktashev等在连续流反应器中研究反应压力对棕榈油超临界反应制备生物柴油的影响,在棕榈油体积浓度为0.155、反应温度为335℃的条件下,反应压力从18MPa提高到27MPa,甘油酯的转化率不断提高,继续提高反应压力到35MPa,甘油酯的转化率却会降低。
He等计算了不同反应压力下的反应常数,在280℃、醇油摩尔比42∶1的条件下,反应压力从12.5MPa提高至32MPa,反应常数从4.55×10-4s-1升至1.12×10-3s-1,从另一个角度解释了压力提高促进反应加快的原因。
2.3 醇油摩尔比
由于酯交换反应为放热反应,超临界反应下的高反应温度虽然有利于加快反应速度,但会降低化学平衡常数。根据计算,当反应温度从25℃提高到300℃时,反应平衡常数从4.485×109大幅降至24.292。为推动反应向生成脂肪酸甲酯的方向移动,获得较大的平衡常数,超临界反应制备生物柴油过程中多加入过量甲醇。过量甲醇的加入可以提高反应底物甲醇的浓度,加快反应速度。
Kusdiana等研究350℃条件下,醇油摩尔比对菜籽油与甲醇反应的影响,发现醇油摩尔比从3.5∶1升至42∶1的过程中,脂肪酸甲酯的收率不断提高。Demirbas等在间歇反应釜中研究醇油摩尔比对棉籽油与甲醇在超临界状态下反应的影响,反应温度为240℃时,醇油摩尔比从1∶1提高到41∶1,甲酯生成速率不断提高;而且醇油摩尔比为9∶1~41∶1的甲酯生成速率显著高于醇油摩尔比为1∶1 和3∶1的反应体系,前者120s左右就能接近平衡,后者300s之后也未达到平衡,这说明过量甲醇对于加快反应速度和提高转化率是非常有效的。
尽管提高醇油摩尔比有利于加快反应速度和提高平衡转化率,但甲醇用量过高也会降低油脂浓度,可能导致反应速率下降;而且,过量甲醇的回收是一个严重的能量消耗过程,所以必须将甲醇用量控制在一定的范围。
Tan等在间歇反应釜中研究醇油摩尔比对超临界酯交换反应的影响,发现醇油摩尔比从20∶1提高到60∶1,精炼棕榈油和废弃的煎炸棕榈油与超临界甲醇反应的甲酯收率都呈现先升后降的趋势,而且最佳醇油摩尔比都是40∶1 左右。
2.4 低碳醇种类
低碳醇作为反应原料之一,其极性、临界参数等性质可能影响超临界反应的活性。
C1~C5正构醇的临界温度和临界压力数据如表1所示,它们与甘油三酸酯在300℃下反应时,脂肪酸酯的生成速率随低碳醇碳链的延长而不断降低,而且甲醇的反应速率显著高于其他低碳醇;不过,与酯交换反应不同,各正构醇与脂肪酸的酯化反应结果上基本没有什么差异。Vieitez等在连续反应器中研究甲醇和乙醇与油脂的超临界醇解反应,在相同反应条件下,甲醇醇解反应都比乙醇醇解反应快很多。
表1 几种低碳醇的临界参数
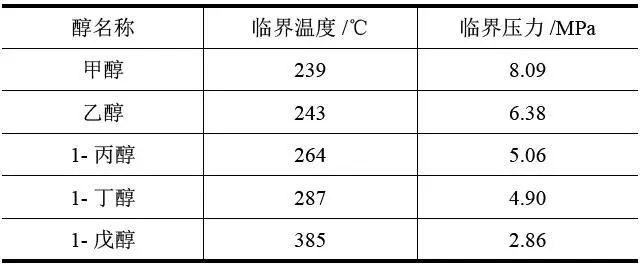
2.5 水 分
在酸、碱催化工艺中,油脂原料中存在的水分和脂肪酸会导致皂化、乳化,显著降低催化效率,但在350℃、醇油摩尔比42∶1、反应4min的超临界反应条件下,菜籽油中水分体积分数从0增至50%过程中,甲酯收率有小幅降低,但都在90%以上。
Vieitez等向大豆中加入10%水分,考察水分对油脂超临界醇解反应的影响,发现加水之后,油脂转化率和甲酯收率都比无水条件下高。Tan等也观察到水分含量在0~20%逐步提高时,甲酯收率不断提高。
Kusdiana等认识到甘油酯与甲醇酯交换反应速率太慢,反应条件太苛刻,开发了超临界水解- 超临界酯化两步反应来制备生物柴油,水解和酯化两步反应都在270℃、20min完成。
在超临界状态下,大量甲醇以缔合态存在,甲醇必须解除缔合成为单分子后才可能继续发生解离,产生具有反应活性的甲氧基基团。当反应体系中存在水时,由于其极性大,更容易与甲醇结合在一起,从而破坏了甲醇缔合体,客观上起到了增加甲醇解离的作用,可以为反应提供更多的活性态基团;水还会与体系中的质子形成相应的质子化物,促进甘油三酸酯和脂肪酸反应,缩短反应达到平衡的时间。
2.6 脂肪酸
游离脂肪酸是未经处理的天然油脂和酸化油、地沟油等废弃油脂中的常见组分,它们在酸催化工艺或碱催化工艺中都会显著影响脂肪酸甲酯的收率。但超临界反应条件下,油酸含量在0~30%变化,对甲酯收率都没有明显的影响。Wang等向超临界反应体系中加入5%~30%的硬脂酸或油酸,观察到甲酯收率的提高,而且提高幅度与添加脂肪酸的量呈正相关性。
Warabi等在300℃下研究甘油三酸酯和脂肪酸与低碳醇反应的速率,发现甘油三酸酯与低碳醇之间的酯交换反应速率明显低于脂肪酸与低碳醇之间的酯化反应速率,而且饱和脂肪酸的酯化反应速率比不饱和脂肪酸低。Ong等计算了350℃下甘油三酸酯和脂肪酸与超临界甲醇的反应活化能,分别为36.01kJ·mol-1和28.38kJ·mol-1,这可能是脂肪酸酯化反应比油脂酯交换反应易于进行的主要原因。
脂肪酸酯化反应的产物是水,体系中存在水时,又会与甘油酯、脂肪酸甲酯发生水解反应。所以,超临界反应制备生物柴油过程中水分和脂肪酸对反应的影响一定是同时存在的。
2.7 反应器及反应形式
超临界流体反应制备生物柴油有两种反应形式:间歇反应和连续反应,两种反应形式的操作流程及结果差别很大。
间歇反应多在耐高压密闭反应器内进行,常见的间歇反应器有管式反应器和釜式反应器。实验时先将一定比例的油脂与甲醇倒入反应器中,然后将反应器浸入高温热源,反应一定时间后取出,快速降温。间歇反应中,反应体系的压力由物料量、反应器体积以及温度共同决定,随着反应的进行,反应体系内物料组成、相态以及压力一直在发生变化,所以难以对压力进行精确控制。但密闭反应器耐温耐压,可以开展极端条件的实验研究。
连续反应则多在管式反应器内进行,反应压力由压控阀控制,与进料量、反应器体积和反应温度无关,所以可实现反应压力的精确控制,反应重复性好,也更适合于大规模生产。Marulanda 等用外径3.175mm、壁厚0.711mm、长8m的管式反应器建立了小型连续超临界反应装置,并对鸡脂超临界反应制备生物柴油工艺进行研究,最佳工艺条件为:400℃、30MPa、醇油摩尔比9∶1、停留时间6min。在400℃的高温下,停留时间小于7min 可以避免热分解。He 等得到连续反应的最佳条件是310℃、35MPa、醇油摩尔比40∶1、停留时间25min ;但此条件下副反应严重,产物收率只有77%,通过梯度加热可将甲酯收率提高到90%。李琪等在外径3mm、壁厚0.51mm、长为2m管式反应器中研究超临界甲醇法连续制备生物柴油工艺,在280℃、14MPa、醇油摩尔比42∶1的条件下反应,120min才能达到收率最大值,但甲酯收率不到50%,推测反应温度过低以及流速过低导致混合不佳。
2.8 过程强化
典型超临界反应工艺温度和压力都非常高,给工业应用带来比较大的障碍,为此不少研究者尝试通过引入共溶剂、使用催化剂、添加超声场等强化反应手段,来缓和反应条件。
向超临界反应体系中引入CO2、丙烷、正己烷、庚烷、一氟二氯乙烷等助溶剂后,混合体系的临界点降低,最佳反应条件的温度和压力就可能更低。在丙烷/甲醇摩尔比为0.05∶1 的条件下,反应温度和压力可降为280°C、12.8MPa,醇油摩尔比也可从42∶1 降为 24∶1,反应10min 后甲酯产率可以达到 97%。同样的效果在CO2作溶剂的超临界甲醇醇解反应体系中也可以观察到,但在乙醇醇解体系中使用 CO2溶剂时并没有观察到统计学意义上的显著变化。
尽管超临界条件下酯交换反应和酯化反应都可以自发进行,但如果向超临界反应体系中加入少量催化剂,如磷酸、KOH、Ca(OH)2等,都可以显著降低反应的苛刻度。例如大豆油间歇反应中加入0.1%的KOH,可将反应温度从350℃降至160℃、醇油摩尔比从42∶1降至24∶1,反应20min后甲酯产率可以达到98%。宋成才等使用K2O/γ-Al2O3作催化剂,可以将反应温度和压力降到180℃、2M~3MPa,在醇油摩尔比为40∶1的条件下反应10min,产物中甲酯浓度可以达到90%。侯相林等使用K2CO3/Al2O3催化剂,在140℃、2MPa、醇油摩尔比16∶1的条件下反应30min,产物中甲酯质量分数也可以达到90%。
Biktashev等在油脂与甲醇高温酯化反应前引入超声场以强化油脂与甲醇的乳化,然后再进行超临界反应,发现在280~355℃的研究区间内,超声强化都提高了油脂的转化率,不过这种提高作用随着反应温度的升高不断下降。
乔宝权等在固定床反应器中分别装填玻璃珠、玻璃弹簧以及θ环填料,由于它们均可强化超临界反应过程中的传热和传质,所以甲酯生成速率都明显优于不使用填料的反应,三种填料强化效果从好到差依次为:θ环、玻璃珠、玻璃弹簧。
2.9 技术经济性
2.9.1 设备投资
在进行深入研究前,可能会认为超临界流体技术生产生物柴油涉及高温高压反应工段,势必提高设备投资成本。实际核算却发现,由于超临界流体工艺取消了传统酸碱催化反应中的催化剂预混罐、预酯化罐、中和反应釜及甘油浓缩罐等,所以设备投资比传统工艺更低。Lee等对比相同原料(废弃植物油)、相同规模(40 000kt·a-1)的碱催化工艺和超临界流体反应工艺的设备投资成本,也发现超临界反应工艺的总投资比碱催化工艺低。
Martinovic等用ASPEN8.8对餐饮废油超临界流体技术生产生物柴油进行技术经济性评估,油脂水解后超临界酯化生产生物柴油的两步反应工艺(250℃ /270℃,8MPa)比直接超临界醇解生产生物柴油的工艺条件更温和(350℃,12MPa),总投资和每吨生物柴油的生产成本也更低一些。生产规模为15 000t·a-1时,两步工艺和一步工艺的投资分别为610 万EUR和580 万EUR,不过两步法生产过程的能耗要高于一步法。
2.9.2 操作费用
生产过程中的能耗是决定操作费用的关键因素,不少人会认为超临界反应温度高,所以操作费用一定非常高。实际情况是,超临界流体反应工艺中的高温物料非常便于热量回收,只要采取合适的热量回收技术,就可以将生产过程中的能耗控制在较低水平,有效控制生产过程的操作费用。
Glisic等计算了精炼油脂超临界工艺和均相碱催化工艺生产生物柴油的能耗(表2),发现两者基本相当。Lee等计算碱催化植物毛油、碱催化废弃植物油和超临界流体废弃植物油生产生物柴油的能耗,分别为2349kW·h·t-1、5258kW·h·t-1、3927W·h·t-1, 这说明对废弃油脂加工而言,超临界流体工艺的能耗比碱催化工艺更低。
表2 每吨生物柴油生产能耗(10 000t·a-1)
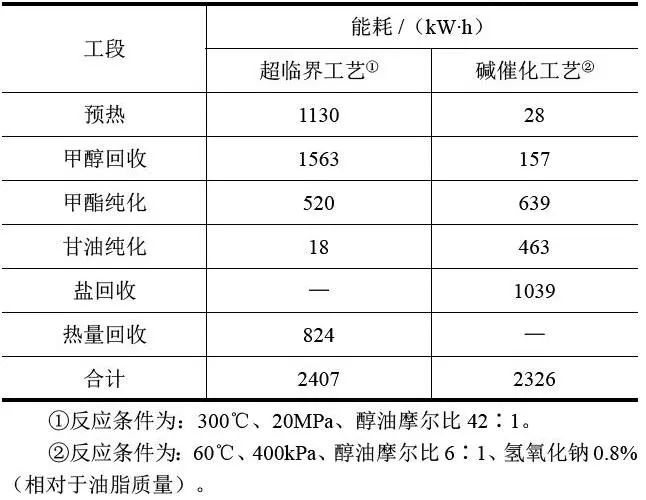
Gutiérrez等计算了丙烷强化的超临界流体生物柴油生产成本,结果表明在保证10%收益率的前提下,超临界流体工艺的生产成本可以与现有酸、碱催化工艺相媲美。计算结果还揭示,采用闪蒸代替传统精馏塔分离甲醇和丙烷可以大幅降低生产过程能耗。
3 超临界流体技术制备生物柴油前景
3.1 超临界流体制备生物柴油的
优势及问题
生物柴油的成本难以降低是影响生物柴油广泛应用的关键因素。在生物柴油的制造成本中,原料成本约占生物柴油总成本的70%~80%,所以降低生物柴油生产的原料成本是提高生物柴油生产经济性的关键。超临界流体技术适合废弃油脂加工生产生物柴油,原料油中的水分、脂肪酸等杂质对反应基本无不良影响,所以开发廉价废弃油脂的超临界流体生产技术对于提高生物柴油的经济竞争力具有重要意义。
在相同规模条件下,超临界流体工艺生产生物柴油的设备投资成本比精炼油脂碱催化工艺要高,但比劣质废弃油脂的碱催化工艺低。当原料油的质量较好时,超临界工艺的生产能耗比碱催化工艺能耗略高;当原料油质量较差,超临界反应工艺无需预处理,能耗比碱催化工艺低很多。
超临界流体技术生产生物柴油不使用酸碱催化剂,所以无需中和、水洗,三废排放显著低于酸、碱催化工艺,工艺的环保优势明显。
不过典型超临界流体工艺的反应条件太过苛刻,成为制约该技术工业化的主要障碍。反应温度过高会增加导热油的采购和使用成本,反应压力过高则会提高泵的采购成本和出现故障的概率,而且其他设备和管线的采购价格也会随着压力等级的提高大幅升高,装置的安全措施也必须相应提高,所以降低反应苛刻程度对于降低投资和运行成本具有重要意义。
多数超临界典型工艺为了追求较高的转化率和较快的反应速度,多使用极过量的甲醇,这是影响工艺技术经济性的关键参数。由于氢键作用,甲醇的汽化潜热很高,沸点低,热量也难以回收利用,这就增加了生产过程的能耗。不考虑热量回收时,超临界反应制备生物柴油工艺中甲醇回收的能耗在总能耗中占比可以达到60%左右;如果考虑热量回收,占比最高可达到81.08%。这使得甲醇回收过程成为超临界反应工艺中温室气体排放最高的环节,有时甚至成为决定工艺能否盈利的关键因素,所以必须降低超临界流体制备生物柴油中的甲醇用量。
3.2 超临界流体技术制备
生物柴油的提升方向
3.2.1 降低生产成本
降低生物柴油的生产成本是生物柴油产业永恒的主题。Marchetti等分析了影响超临界工艺生产生物柴油成本的主要因素,按贡献程度从高到低依次为:原料价格、生产规模、副产品甘油的价格和投资成本。
使用低成本的废弃油脂,如酸化油、地沟油等,是降低生物柴油生产成本最有效的措施,而且废弃油脂中的水分、脂肪酸等杂质对超临界反应基本没有负面影响,不少条件下甚至显示出加快反应速率、提高产品收率等正面效果,所以越来越多的生物柴油工厂选择废弃油脂作为生产原料。
超临界工艺生产生物柴油的流程模拟结果表明,扩大生物柴油生产规模可有效降低单位质量生物柴油的生产成本,所以在保证原料供给的前提下,应尽量扩大生产规模。
在甲醇用量确定后,对超临界流体工艺生产生物柴油过程中的物料进行热量回收亦可显著降低生产过程的能耗,尤其是在工艺设计阶段设计合理的换热网络和热量回收工艺对于降低生产成本至关重要。
3.2.2 降低反应苛刻度
使用共溶剂是降低反应苛刻度的有效技术,不过对实际工业过程而言,这并不是一个非常好的选择。首先,向任一反应体系引入新组分都需要增加对该组分的分离和回收利用单元,这就必然意味着工艺流程的复杂化和投资成本、运行成本的增加;而低沸点共溶剂分离回收过程中的低品位热量难以回收,所以能耗也必然会增加。
使用催化剂也可以大幅度降低反应温度和压力,但应尽量避免使用均相催化剂,因为在反应过程中使用均相催化剂后,就需要采用中和、水洗或吸附等措施分离出催化剂,这就必然会产生废液和废渣,这样就失去了超临界反应工艺绿色、环保的优势。开发合适的非均相催化剂才是值得研究的降低反应苛刻度的方向,不过需要注意的是,非均相催化剂仅仅适合于油脂原料油,对废弃油脂而言,由于原料中难免存在脂肪酸、胶质以及机械杂质,使用非均相催化剂时,很容易出现杂质在催化剂床层积累,导致床层压降升高以及催化剂失活等问题。
石油化工科学研究院在连续管式反应器中研究多种原料油与甲醇的超临界反应,在260℃、8MPa、醇油摩尔比18∶1、反应时间60min的条件下,发现酸值高的原料油都可以达到90%以上的收率,而酸值低的几种原料油,生物柴油收率则较低。在进一步的研究中,发现调节原料油的酸值不低于50mgKOH·g-1的条件下,都可以实现在缓和条件下获得较高甲酯收率的目标,反应压力还可进一步降低至6MPa的近临界区间。与典型的连续超临界反应工艺相比,不仅反应条件明显缓和,甲醇用量也大幅降低,是工业上低成本降低反应苛刻度的有效措施。
3.2.3 连续化、大型化
早期超临界反应制备生物柴油的研究多采用间歇方式进行,但间歇生产的单位空时产率低,生产过程也不稳定,因而以连续反应代替间歇反应是生物柴油工业化的必然要求。
汪铁林等开展了百吨级超临界连续化制备生物柴油的单管扩大试验,并与实验室小试试验进行对比,发现在相同工艺条件下,扩大试验装置中的甲酯收率比相同反应时间内(0~30min)小试试验高25%左右,作者将其归因于雷诺系数提高,传质得到改善所致。
石油化工科学研究院则完成了连续法近/ 超临界反应制备生物柴油技术的实验室小试、中试(2000t·a-1)和工业试验(60 000t·a-1),不同规模的甲酯收率都在94%左右,证明连续工艺的稳定性,也验证了该技术的稳定性和可行性。
4 结 语
超临界流体独特的物理化学性质使其可以对化学反应产生多方面影响,超临界甲醇在高温条件下发生解离和质子化产生甲氧基离子和质子化甲醇然后攻击甘油三酸酯的酰基是酯交换反应在无催化剂条件下也能进行的主要原因,高温增加反应物中活化分子的比例也是超临界反应能快速完成的原因之一。
反应温度、压力、低碳醇种类和用量、原料油中的水和脂肪酸以及反应器等因素都是影响超临界反应的重要因素;向反应体系中引入共溶剂、使用催化剂或添加超声场等都可以强化反应过程,缓和反应条件。对超临界流体制备生物柴油的技术经济性分析表明,超临界流体技术制备生物柴油的设备投资和操作费用均可与常见的碱催化工艺相竞争。
超临界流体制备生物柴油技术具有原料适应性好、技术经济性好、生产过程清洁等优点,是值得重点发展的生物柴油生产技术。使用廉价的废弃油脂、减少甲醇用量和开展热量回收是降低生物柴油生产成本的主要措施。对优质和劣质油脂原料分别采用非均相催化和调节原料酸值是较为合适的降低反应苛刻度的方法。连续化和大型化则是超临界制备生物柴油技术工业化的必然要求。
全文刊登于《生物产业技术》2019年第5期