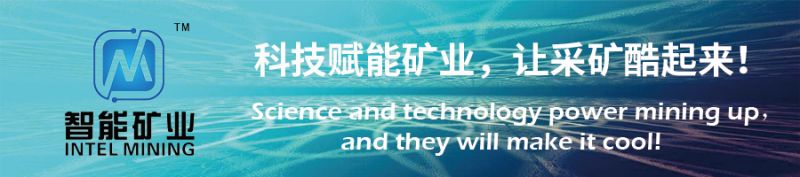
供稿:峯斯基
智能化开采是指在不需要人工直接干预的情况下,通过采掘环境的智能感知、采掘装备的智能调控、采掘作业的自主巡航,由采掘装备独立完成的回采作业过程。智能化开采是在机械化开采、自动化开采基础上,信息化与工业化深度融合的煤炭开采技术变革。因此,智能化开采具有3个技术内涵:
①采掘设备具有智能化的自主采掘作业能力;
②实时获取和更新采掘工艺数据,包括地质条件、煤岩变化、设备方位、开采工序等;
③能根据开采条件变化自动调控采掘过程。
当智能化采掘设备与自动调度决策集为一体,即形成无人化开采工作面。
国外研究现状综述
目前,在以“智能化”为核心的综采工作面开采技术方面,美国、德国和澳大利亚的煤炭企业发展较早,综采工作面智能化的研究取得了一定的成功,通过采用计算机技术、采煤机记忆截割技术、电液控制技术和变频软启动技术等,在地质条件好的中厚煤层实现了工作面3~5人的全自动化割煤,并探索实现工作面无人的智能化开采。
20 世纪 90 年代以来,美国、英国、德国、澳大利亚等国开始着手研究自动化综采关键技术,并取得了一些显著性的成果。德国 DBT 公司成功的研制了基于 PM3 电液控制系统的薄煤层全自动化综采系统。美国JOY 公司开发了基于计算机集成的薄煤层少人操作切割系统。进入21 世纪以来,国外煤矿开采追求“安全、高效、简单、实用、可靠、经济”的原则,其智能开采的技术思路是: 通过钻孔地质勘探和掘进相结合的方式,描绘工作面煤层的赋存分布,通过陀螺仪获知采煤机的三维坐标,两者结合实现工作面的全自动化割煤。该思路可避开煤岩识别难题,以地质条件为载体,顶层规划自动化采煤过程。
1工作面自动化LASC 系统2001 年7 月,澳大利亚联邦科学与工业研究组织CSIRO 承担了ACARP( Australian Coal Association Research Program,澳大利亚煤炭协会研究计划) 设立的综采自动化项目,开展综采工作面自动化和智能化技术的研究。到2005 年该项目通过采用军用高精度光纤陀螺仪和定制的定位导航算法取得了3项主要成果,即采煤机位置三维精确定位(误差±10cm)、工作面矫直系统(误差±50cm)和工作面水平控制,设计了工作面自动化LASC系统,并首次在澳大利亚的Beltana矿试验成功。2008年,对LASC系统进行了优化,增加了采煤机自动控制、煤流负荷平衡、巷道集中监控等,在商业应用方面CSIRO 研究组同久益、艾可夫等采煤机供应商签署了协议,将这项技术集成到对应的采煤机上,实现快速商用。LASC系统包含惯性导航系统和工作面自动控制算法2 项核心技术。
(1)LASC 系统将基于光纤陀螺的惯性导航设备安装在采煤机机身电控箱内,通过运行嵌入式导航定位软件实现采煤机三维位置的精确定位。该惯性导航定位软件在无GPS信号辅助的情况下行进2.7km,定位误差在30cm以内。惯性导航定位软件可用于综采工作面的水平控制和连续采煤机自动制导。
①对于综采工作面水平控制,基本原理是首先根据巷道掘进数据和钻孔数据生成工作面三维地质模型,该模型精度能达到50mm,能准确反映出煤层起伏、倾角、断层等构造,可直接用于指导采煤机俯仰采控制。然后利用在采煤过程中记录的顶底板位置信息对该模型进行不断优化,就可以准确预知工作面的煤层变化情况。其次结合采煤机精确定位软件的数据,LASC系统就能够提前控制采煤机的割顶割底量,从而顺利通过断层等地质变化区段。澳大利亚煤矿使用的水平控制开采技术控制原理如图2.1 所示。
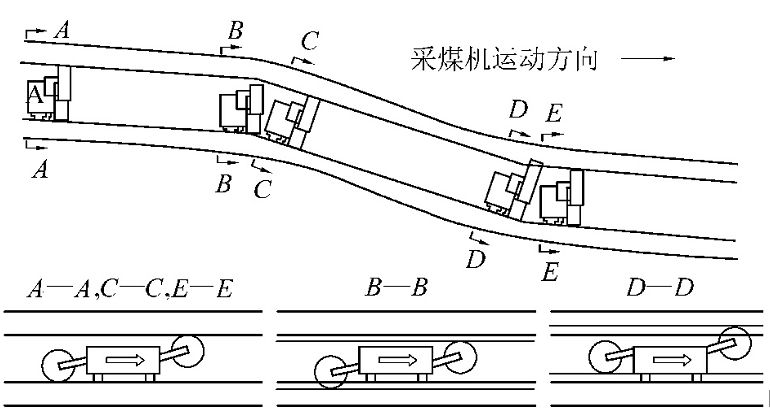
图2.1 澳大利亚煤矿使用的水平控制开采技术控制原理
②连续采煤机自动制导,已被澳大利亚确定为煤炭产业重要的技术。基于连续采煤机自动制导技术开发了具有应用程序控制和通信功能,且包含先进图形用户界面的自动制导系统,如图2.2 所示,表示连续采煤机偏航角有了一定的误差,需要在后面的开采中实时校正。
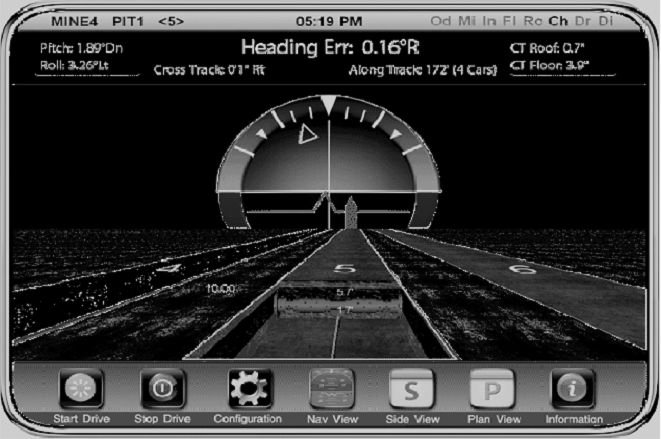
图2.2 连续采煤机出现偏差的导航
(2)工作面自动控制模型和算法。基于该算法,设计了工作面矫直系统,其包含高精度舵性导航仪和矫直数据分析系统2 项核心技术,通过对舵性导航仪记录的采煤机空间位置进行分析,确定当前工作面的直线度,计算出每台液压支架的推移量,给液压支架电控系统发出执行信息,对工作面直线度进行动态调整。惯性导航仪输出2 路信号: 一路给支架,控制支架的推移量; 另一路给采煤机,用于控制采煤机的割顶割底量。自2009 年惯性导航仪开始商业化应用以来,澳大利亚60% 以上的综采工作面使用了工作面矫直系统。
2 智能开采服务中心智能开采服务中心作为一种增值产品/服务,在澳大利亚布里斯班的Anglo 矿业公司总部设置总调度室,对所管辖矿井进行实时监控,目前只有莫兰巴北矿上线。
根据出现的报警、故障信息,及时发邮件或电话通知矿井进行调整。同时,每日、周、月和季度向矿井提交运行分析报告,指导矿井提高运行管理水平,合理安排设备检修。分析报告包括每日的触发响应动作计划通知,每周的智能服务回顾,每月的井下精益运行回顾,每季度的生产表现回顾。智能开采服务中心的应用可以实现停机时间少、早期监测和设备损坏最小化,可提高生产力,降低生产成本。
3布尔加( Bulga) 井工矿智能开采技术布尔加( Bulga) 井工矿属于澳大利亚嘉能可 ( Glencore) 矿业开采公司,属高瓦斯矿井。2013年产量740万t,2014年计划产量810万t,单井单面。属于LW2层面第5 个工作面,工作面长度405 m,走向长度3471 m,工作面采高3.0~ 3.2m,设计产量3500 t /h。全套开采装备包括:7LS6D 采煤机,RS20S 液压支架控制系统,2台11 kV 和1.6 MW刮板输送机电动机,6台INOXIHP泵站(泵站压力32. 5~34.5MPa的4台,40.0~41. 5MPa的2台)。采煤机智能控制系统为Faceboss,工作面自动化系统为LASC。
每星期进行2 次检修,分别是星期二的7: 00-14: 30 和星期五的7: 00-17: 30,其他时间安排生产。实行三八制,早班7: 00-15: 00,中班15: 00-23: 00,夜班23: 00-次日7: 00。每生产班人员10人,分为正副班长(2人)、电工(2人)、机械工(2人)、操作工(3人)和维护主管(工程师1人)。
采煤机从刮板输送机机尾到机头时,采煤机司机控制顶滚筒、底滚筒随动割煤。而从机头到机尾时,采煤机根据上一刀信息自动记忆割煤,重载速度8~14 m/min。支架采用自动拉架+人工干预方式 (顶板破碎,人工超前拉架),立柱安装2个压力传感器,一用一备。工作面矫直系统在割煤过程中实时记录采煤机三维位置、横向和纵向倾角,采煤机每截割4刀时,矫直系统根据记录的信息,控制每台支架的推移量,调节工作面的直线度。
LASC 系统的应用使矿井煤炭产量提高了5%~25%,减少工人暴露在高危工作环境的时间,提高矿井安全水平;同时减小了煤炭产量波动,达到了均衡生产,提高了矿井生产质量管理水平。