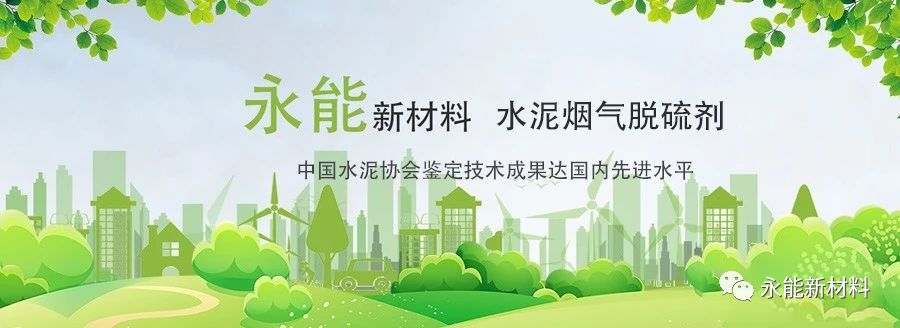
在固定床脱硫实验平台上探究低温低含水率条件下,制备钙基脱硫剂的脱硫过程及脱硫机理。采用BET表征手段对脱硫剂的孔隙结构进行表征,X射线能谱分析脱硫剂中活性氧化钙的含量。结果表明:根据脱硫反应速率与扩散速率的差值,将钙基脱硫剂的脱硫过程分为动力段、平衡段和过渡段三个阶段,脱硫效率在动力段由脱硫反应速率控制,在过渡段由气体扩散速率控制,提高脱硫效率即减小脱硫反应速率与气体扩散速率的差值;随着含水率的增加,有效脱硫时间和最大脱硫效率分别呈现递增和递减的趋势,本实验中脱硫效率最大为100%,有效脱硫时间最长为55.47 min,粉煤灰和熟石灰掺混比(质量比)不同的脱硫剂有效物质含量以及脱硫剂孔隙结构均发生变化,最佳掺混比为3∶1;在过渡段中存在脱硫效率的小幅度上升,当含水率越小,粉煤灰占比越大过渡段脱硫效率的上升趋势越明显,上升段主要发生在中小孔径区域。0 引 言目前,电站锅炉和工业锅炉是二氧化硫的重要来源。石灰石-石膏法在电站锅炉中广泛应用,其技术已经相对成熟。半干法脱硫工艺对于中小型锅炉有很好的适应性,而半干法脱硫剂活性是决定该工艺脱硫效果的核心因素。半干法脱硫技术多采用低硫煤为原料,而燃烧后产生的粉煤灰具有高碱性,因此在一定的含水率下,粉煤灰中的Si离子和Al离子从水中溶出与掺入的熟石灰发生胶凝反应,最终生成水合硅铝酸钙。因水合物质具有比表面积大和持水性高等特点,可通过一定的配比和加工工艺制备出具有较高活性的脱硫剂。煤炭科学研究总院结合反应动力学原理及半干法脱硫工艺,研发出高倍率灰钙循环(NGD)脱硫技术,通过利用高速热烟气流中的SO2与脱硫剂中的碱性活性物质充分接触并发生反应,从而达到脱硫目的。LI et al对半干法钙基脱硫剂性能进行了大量研究。脱硫剂制备流程为:将原始样品与水混合制成脱硫剂浆液,之后进行水合反应,再进行真空抽滤、干燥、压饼保存或者在红外干燥器中将滤饼制成粉末进行保存以供脱硫使用,但该制备方法操作繁琐,在工程上应用经济性差。为将脱硫剂制备与半干法脱硫工艺有机结合,本实验以粉煤灰为原料,在低温、低含水率条件下制备吸附剂。在固定床上对脱硫剂的性能进行表征,分析了半干法脱硫机理以及脱硫剂制备条件对脱硫性能的影响,以期为提高脱硫效果提供理论参考。1 实验部分1.1 样品表征以神东哈拉沟30 t/h煤粉锅炉烟道口未经脱硫的原始灰和工业熟石灰作为原材料。粉煤灰的主要成分见表1。采用ESCALAB 250Xi型X射线能谱(XPS)分析仪测量原材料的表面元素以及Ca元素的不同形态和含量,结果见表2和表3。由表2和表3可知,原材料中活性氧化钙的含量较高,适合脱硫,熟石灰中含有少量的CaCO3,主要原因是熟石灰是由CaCO3高温煅烧而成,含有少部分未分解的CaCO3。表1 粉煤灰主要成分
Table 1 Main components of fly ash

表2 原始样品表面的元素分析
Table 2 Ultimate analysis of original samples surface
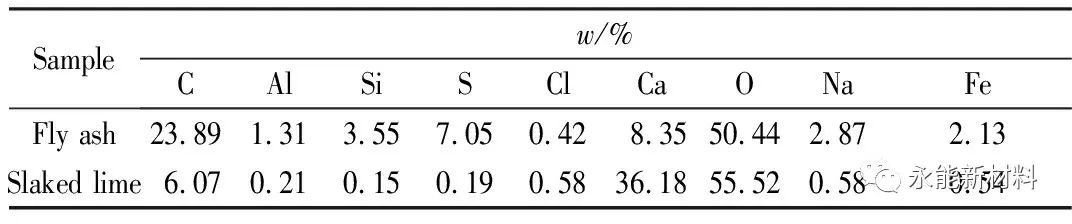
表3 原始样品中Ca元素的形态和含量
Table 3 Form and content of Ca in original sample

1.2 脱硫剂制备半干法钙基脱硫剂采用粉煤灰辅助以熟石灰钙基碱性物质为原料进行制备。首先将原材料进行干燥,按照粉煤灰和熟石灰掺混比(质量比)分别为1∶0,3∶1,1∶1,1∶3,0∶1进行混配,然后添加一定质量的增湿水使脱硫剂中含水率(水分质量与脱硫剂总质量的比值)分别为5%,10%和15%,最后在水合反应器中充分搅拌3 h后制得。1.3 脱硫实验装置及评价指标固定床脱硫反应实验装置见图1。为防止脱硫剂结团以及出现烟气短路现象,将10 g脱硫剂与20 g石英砂充分混合填充在U型管气固两相反应器内,油浴锅升温至70 ℃时,读取油浴锅温度计示数。当温度符合实验条件,打开反应器旁通阀,依次打开N2,O2和SO2气体钢瓶,使用微量调节阀调节气体至相应流量,通过U型管气体预热器预热并充分混合。进入稳定工况后,关闭反应器旁路,打开U型管脱硫反应器,进行脱硫实验。采用testo 350烟分仪读取出口气体成分,观察到脱硫效率低于50%时,脱硫实验停止。收集反应后的脱硫剂,采用MicroActive for ASAP 2460型氮分析仪对样品进行BET比表面积表征。
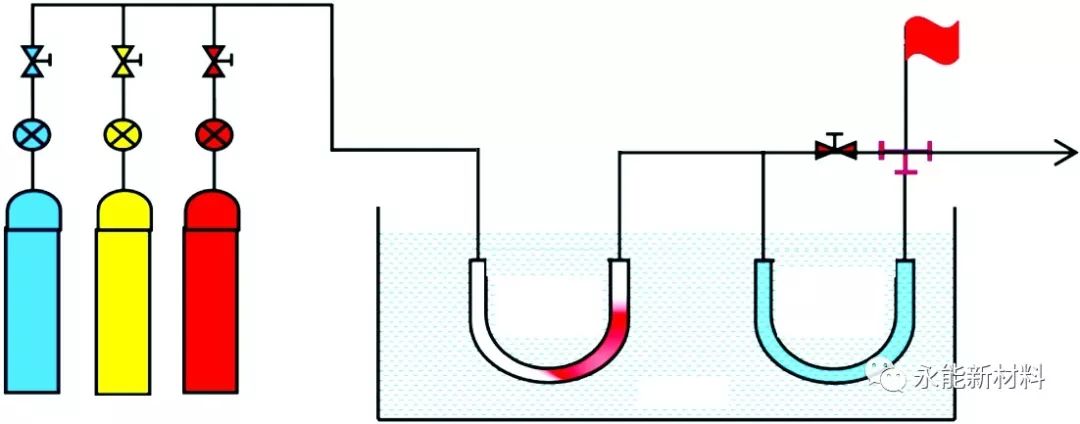
图1 脱硫实验装置
Fig.1 Desulphurization device diagram实验中,通过测量反应器进出口SO2的体积分数计算脱硫效率ηds,脱硫效率计算公式为:
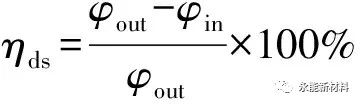
式中:φin为反应器进口SO2体积分数,μL/L;φout为反应器出口SO2体积分数,μL/L。入口烟气中N2流量为1 600 mL/min,O2占气体总体积的5%,SO2的体积分数为200 μL/L时,总流量为1 684.6 mL/min,反应器体积即脱硫剂与石英砂混合之后的体积,实验中反应器体积为30 mL,固定床填料孔隙率按0.5计,则脱硫剂物料实际体积为15 mL,停留时间为0.53 s。本实验中有效脱硫时间选取为脱硫效率由0增加到最大脱硫效率再降到脱硫效率为50%的运行时间,最大脱硫效率为脱硫过程中脱硫效率出现的最大值。2 结果与讨论2.1 脱硫过程分析在粉煤灰与熟石灰掺混比为1∶0、含水率为15%、水合搅拌为3 h条件下制备脱硫剂。在固定床反应器上进行脱硫实验并分析脱硫剂的脱硫过程。脱硫温度为70 ℃,SO2的体积分数为200 μL/L,脱硫效率随运行时间的变化曲线见图2。本实验根据脱硫效率与扩散速率的大小关系将脱硫效率曲线分为三个区域:动力区(AB段)、平衡区(BC段)和过渡区(CD段)。半干法脱硫属于液相间的离子反应,SO2的脱除主要体现在两方面,一方面是在脱硫剂表面发生物理吸附和化学吸附,另一方面是水分可溶解部分SO2。
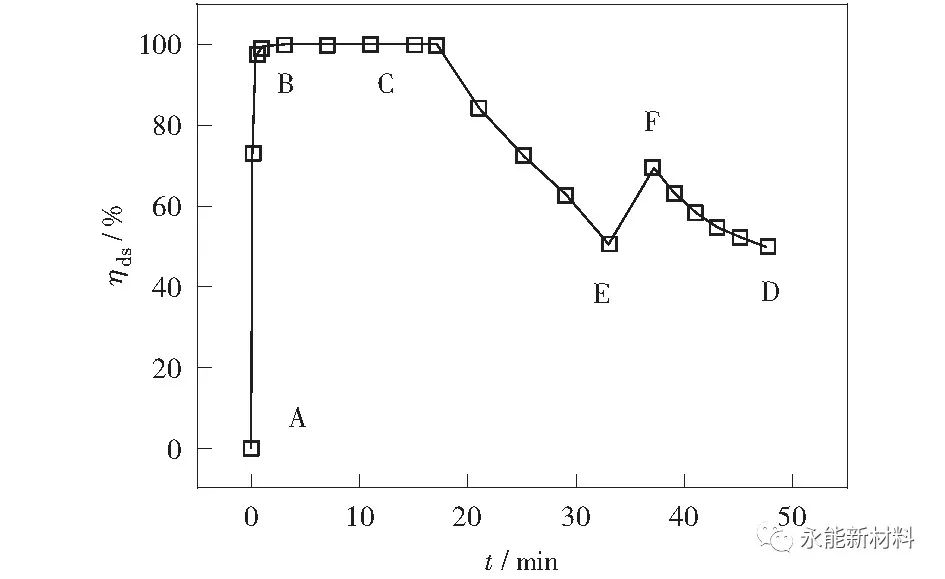
图2 运行时间对脱硫效率的影响
Fig.2 Effect of running time on desulfurization efficiency由图2可知,在AB段脱硫初始阶段,脱硫剂表面被增湿水覆盖,使钙离子溶解。在反应初期迅速发生脱硫反应且在此阶段脱硫剂的孔隙没有被产物堵塞,有利于脱硫反应的进行。此时,在脱硫剂表面SO2的体积分数最高,脱硫反应首先发生在脱硫剂表面,由于摩尔体积VCaSO3约为摩尔体积VCa(OH)2的1.8倍,所以脱硫剂表面小部分区域由于膨胀形成颗粒状的凸起结构,导致扩散阻力增加,扩散速率减小。当扩散速率减小至与脱硫反应速率相等时,达到最大脱硫效率(图1中B点)。之后脱硫反应进入平衡区(BC段),并在一段时间内维持最大脱硫效率。随着脱硫反应的继续进行,反应区域不断扩大,脱硫剂表面膨胀度趋于一致,逐渐形成连续致密的产物层,使扩散阻力增加,脱硫效率缓慢下降,脱硫反应进入过渡区(CD段),此时气相向固相的扩散成为控制步骤,直到脱硫效率下降到50%,脱硫反应结束。由图2还可以看出,脱硫曲线过渡区(EF段),在过渡段脱硫效率有小幅度上升。在钙基脱硫剂的相关研究中鲜有提及此现象。由于脱硫剂的结构和性质与脱硫剂的制备条件息息相关,因此,整个脱硫过程不同。为探索EF段产生的原因,主要考察脱硫剂制备条件对其的影响,下面将分别研究含水率以及掺混比对EF段的影响,并找到EF段可能发生的孔径范围。2.2 含水率对EF段的影响在不同含水率(分别为5%,10%和15%)、粉煤灰和熟石灰的掺混比为3∶1、水合时间为3 h条件下,脱硫剂的脱硫效率随运行时间的变化曲线见图3。由图3可知,有效脱硫时间随着含水率的增加而增加。当含水率为15%时,有效时间最长,但最大脱硫效率比其他含水率对应最大脱硫效率有小幅度下降。主要原因是,含水率增加使覆盖在脱硫剂表面的增湿水变多,使溶解在水溶液中的钙离子数量增加。根据传质理论,脱硫反应右移,因此含水率越大脱硫产物生成速率越快,使脱硫剂表面迅速形成产物层,扩散阻力增加速率很快。根据2.1节对脱硫反应过程的描述,当脱硫反应速率与扩散速率差值越小,脱硫效率越大。所以含水率越大,脱硫反应速率与扩散速率差值增加,最大脱硫效率降低。但含水率增加,用于脱硫反应的增湿水量增加,所以有效脱硫时间增加。
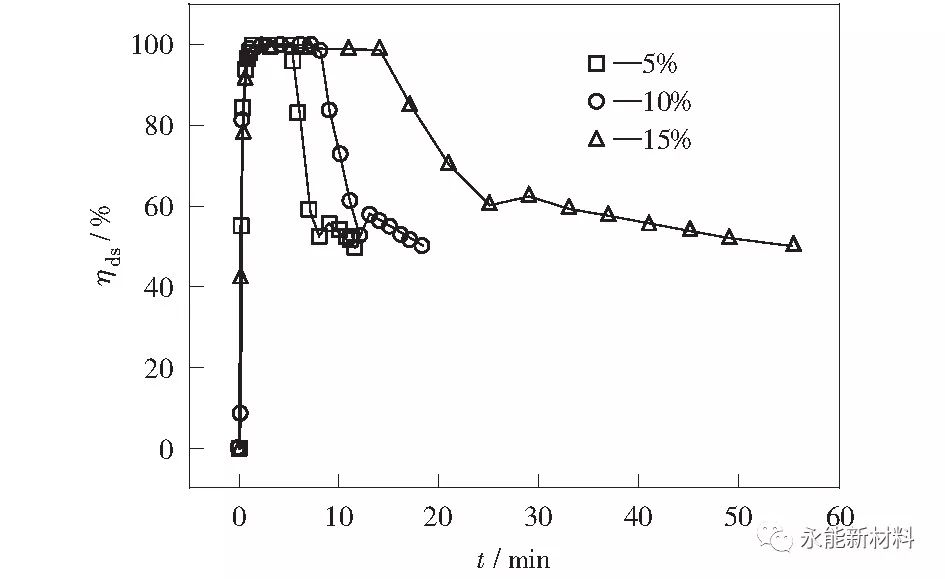
图3 不同含水率下脱硫剂的脱硫效率曲线
Fig.3 Desulphurization efficiency curves of desulfurizer under different moisture contents由图3还可以看出,当含水率为5%和10%时,EF段的变化幅度很大。相比之下,当含水率为15%时脱硫曲线中EF段的变化趋势很小。因此,EF段的上升与脱硫剂制备过程中含水率关系密切,含水率越小,EF段上升趋势越明显。LIU et al制备脱硫剂时水固质量比大于10,因此没有发现脱硫曲线中的EF段。主要原因是,当制备条件为浆液时,脱硫剂表面可充分被水膜包裹,而本实验中增湿水量较小。当含水率为15%时,增湿水总体积小于脱硫剂体积,所以在反应初期脱硫剂表面没有被水膜充分包裹。实验中脱硫反应首先发生在脱硫剂表面有水分存在的位点,并且表面反应与脱硫剂内部反应同时发生。在脱硫反应的动力区和平衡区,表面反应起主导作用。在脱硫反应后期的过渡区脱硫剂表面只是被局部产物覆盖,此时脱硫剂表面大部分水分被反应消耗,气体扩散到脱硫剂内部,利用孔隙内部水分以及活性物质发生反应与高含水率下制备的脱硫剂相比更容易。所以本实验中出现EF段脱硫效率有小幅度上升。将EF段中脱硫效率随时间的变化趋势与整个脱硫过程对比,发现整体变化趋势类似,由于EF段过程中脱硫剂孔隙内部水量相比于反应初期脱硫剂表面的水量少,所以脱硫效率变化幅度小,因此,也可以进一步证明EF段是由增湿水量导致的。2.3 脱硫剂孔隙结构对EF段的影响2.3.1 掺混比对EF段的影响在脱硫反应后期,烟气能够扩散到脱硫剂内部孔隙中与结合水发生脱硫反应,这与脱硫剂的孔隙结构有很大关系。为验证脱硫剂孔隙结构对EF段的产生有影响,在固定床脱硫台架上进行了不同掺混比下的脱硫实验。在含水率为15%,水合时间为3 h,粉煤灰和熟石灰的掺混比分别为1∶0,3∶1,1∶1,1∶3,0∶1时,脱硫实验结果见图4。
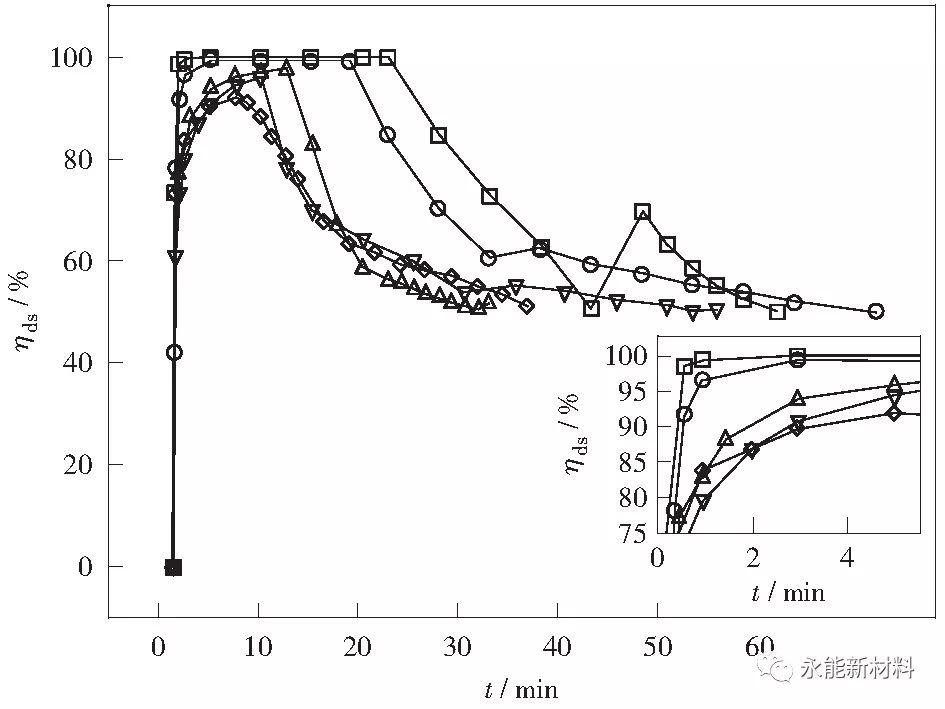
图4 粉煤灰和熟石灰不同掺混比下运行时间随脱硫效率的变化曲线
Fig.4 Variation curves of operation time with desulph-urization efficiency at different mixing ratios of fly ash and slaked lime
□—1∶0;○—3∶1;△—1∶1;▽—1∶3;◇—0∶1由图4可以看出,当粉煤灰和熟石灰掺混比为3∶1时,脱硫效果最好。这说明,经过水合反应之后的脱硫剂脱硫性能优于将熟石灰单独作脱硫剂的脱硫性能。水合物质的产生促进了脱硫反应的进行。本实验的最佳掺混比也在文献[15]中得到验证。当粉煤灰和熟石灰掺混比分别为1∶0和3∶1时,均有EF段的存在,且粉煤灰的质量分数越大,EF段变化趋势越明显。证明了EF段的产生与粉煤灰本身的结构和性质有关,主要是粉煤灰中活性物质的含量以及孔隙结构对EF段的影响。本实验中所使用粉煤灰的活性物质含量与文献所使用原材料进行对比之后发现差别不大,因此,粉煤灰的孔隙结构对EF段产生主要影响。2.3.2 脱硫剂原材料表征分析为检测两种原材料的孔结构参数,对干燥后的原料进行了BET测试。粉煤灰和熟石灰的吸附曲线见图5。由图5可知,根据IUPAC对等温线的分类,粉煤灰和熟石灰的吸附曲线属于Ⅱ型等温线的特点,该类曲线多发生在非多孔性固体表面或大孔固体上自由的单一多层可逆吸附过程。在p/p0=0.1处有拐点,是等温线的第一个陡峭部,它指示单分子层的饱和吸附量,相当于单分子层吸附的完成。随着相对压力的增加,开始形成第二层,当相对压力为饱和蒸气压时,吸附层数无限大。由图5还可知,在p/p0=0.48时,出现分离,形成“迟滞回线”。根据IUPAC对迟滞回线的分类属于H1型,说明两种原孔径尺寸分布较为均匀,属于较窄的介孔材料,且由球形颗粒聚集而成。
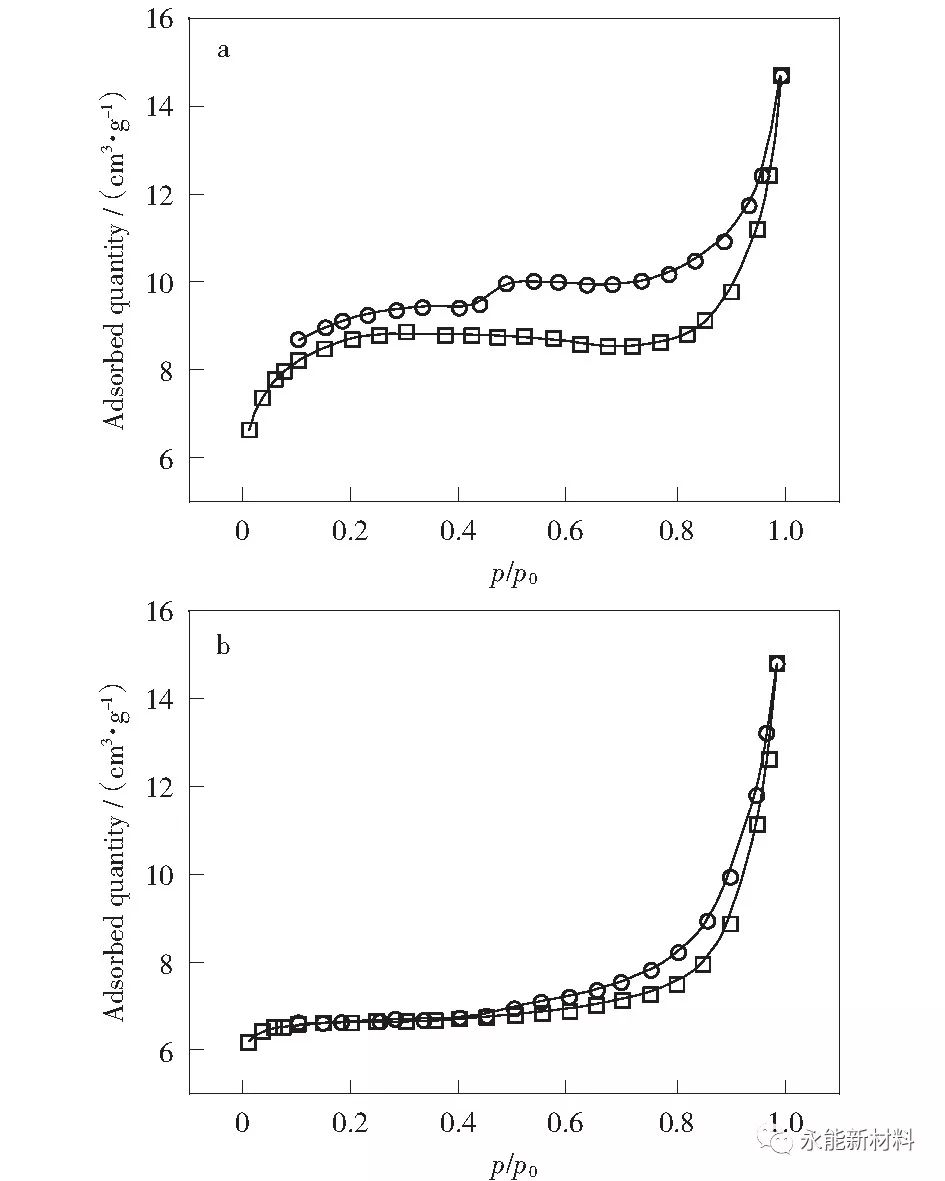
图5 粉煤灰和熟石灰的吸附-脱附曲线
Fig.5 Adsorption-desorption curve of fly ash and slaked lime
a—Fly ash;b—Slaked lime
□—Adsorption;○—Desorption表4所示为粉煤灰和熟石灰的孔隙结构参数。由表4可知,粉煤灰的比表面积大于熟石灰的表面积,粉煤灰的孔体积和平均孔径小于熟石灰的孔体积和平均孔径。为便于叙述,根据孔隙变化趋势将孔分为三种:孔径大于64 nm的孔称为“大孔”,孔径小于6 nm的孔称为“小孔”和孔径在6 nm~64 nm的孔称为“中孔”。表5所示为粉煤灰和熟石灰的孔径区间分布。由表5可以看出,熟石灰孔径分布更集中,而粉煤灰孔径分布分散,小孔和大孔所占比例更大,中孔所占比例小于熟石灰的中孔所占比例。由于脱硫系统压力小于0.1 MPa,当脱硫剂孔径大于100 nm时属于分子扩散,当孔径小于100 nm时属于Knudsen扩散。当气体扩散为Knudsen扩散时,脱硫温度一定,在一定孔径下,扩散速率与孔径成正比,此时气体与脱硫剂壁面碰撞几率越大,烟气与脱硫剂壁面活性物质接触的几率也变大,脱硫反应速率越快。当气体扩散为分子扩散时,气体扩散速率与孔径无关。对于脱硫剂较小孔径,脱硫反应速率大于气体扩散速率,脱硫剂孔隙很快被反应产物堵塞,导致脱硫剂中小孔隙发生破裂和膨胀。所以过小的脱硫剂孔径不适合脱硫,但脱硫剂孔径与比表面积成正比。在孔径分布达到最佳值时,在一定孔隙率下,比表面积存在最佳值,存在适合脱硫反应的有效孔径。因此,通过对比不同脱硫剂反应前后孔径的变化情况,得到脱硫反应的有效孔径范围,最终获得EF段上升的原因。表4 样品的孔隙结构参数
Table 4 Pore parameters of samples

表5 样品的孔径区间分布
Table 5 Pore size distribution of samples
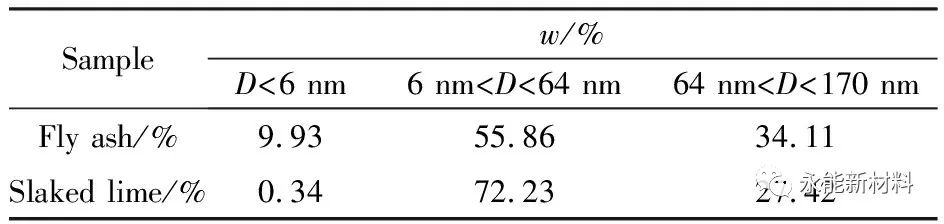
2.3.3 EF段发生的可能孔径为研究脱硫反应前后脱硫剂的孔隙结构参数变化,取粉煤灰和熟石灰的掺混比分别为3∶1,1∶1和0∶1时,反应前后脱硫剂的孔隙结构参数见表6。由表6可以看出,反应前后脱硫剂孔容基本相等,而比表面积及平均孔径差距较大,在反应后平均孔径增加、比表面积和比孔容积减小。不同掺混比脱硫剂反应前后的孔径变化见图6。由图6可以看出,反应前后几种脱硫剂孔径变化趋势类似,脱硫反应前曲线中均存在两个或两个以上峰,但脱硫反应后孔径趋于集中最终孔径以中孔为主。主要原因是,小孔在反应中很快被堵塞膨胀和破裂,而大孔在反应中被产物堵塞变为中孔。根据不同孔径的变化趋势可得到几种掺混比下脱硫剂的有效孔径,孔数量减少说明该孔径参加脱硫反应为有效孔径,对于增加的孔径是否参加脱硫反应尚无定论,但其产生的原因是大孔被产物堵塞。粉煤灰和熟石灰不同渗混比下脱硫剂的有效孔径见表7。由表7可以看出,脱硫反应的有效孔径主要为小孔和中孔。该结论与文献[18]的结论一致,脱硫反应主要发生在孔径D<8 nm及15 nm≤D≤21 nm的区域中。表6 脱硫反应前后不同掺混比脱硫剂的孔隙结构参数变化
Table 6 Variation of pore structure parameters of desulfurizer at different mixing ratios before and after desulfurization reaction
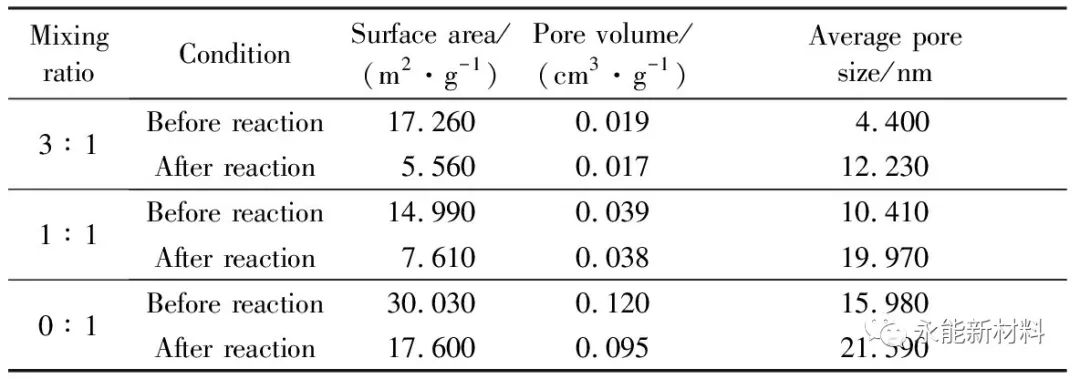
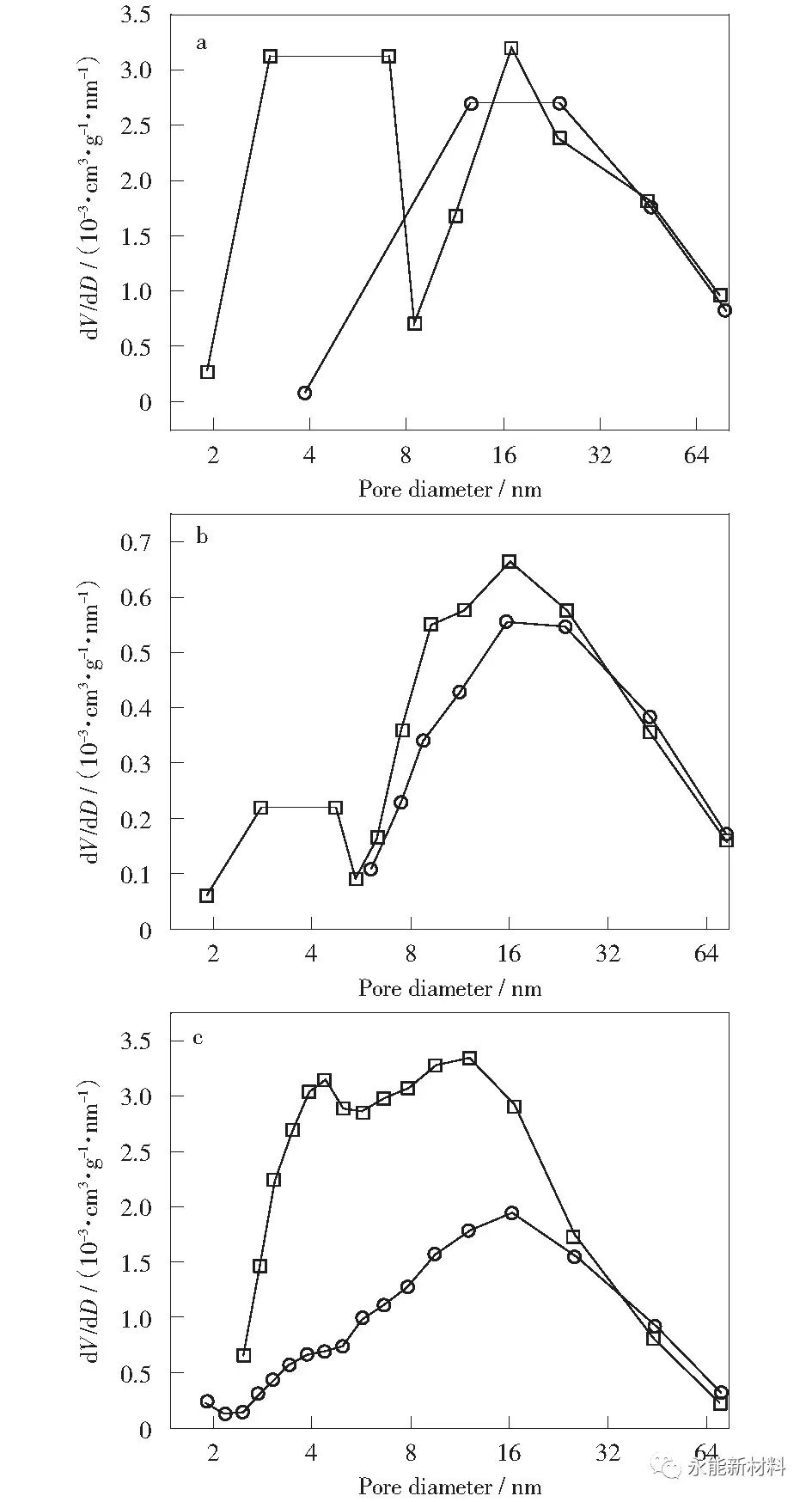
图6 掺混比脱硫剂反应前后的孔径分布
Fig.6 Pore size distribution of desulfurizer at different mixing ratios before and after reaction
a—3∶1;b—1∶1;c—0∶1
□—Before reaction;○—After reaction表7 不同掺混比脱硫剂的有效孔径
Table 7 Effective pore size of desulfurizer at different mixing ratios
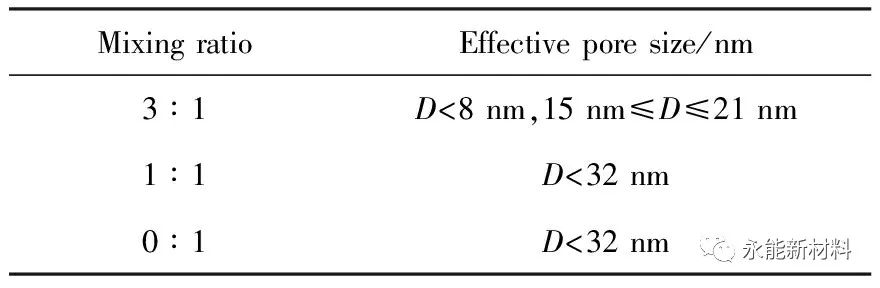
3 结 论1) 动力区和平衡区脱硫阶段的脱硫效率由脱硫反应速率控制,过渡区的脱硫效率由扩散速率控制。因此,提高脱硫效率的途径是减少脱硫反应速率与气体扩散速率之间的差值,即减小动力区的反应速率和提高过渡区的气体扩散速率。2) 对于脱硫剂的制备条件,含水率越小,粉煤灰质量分数越高,反应前脱硫剂的平均孔径越小,过渡区的上升趋势越明显。3) 由于本实验中含水率小,脱硫剂部分表面被脱硫产物覆盖,在过渡区气体可利用脱硫剂孔隙中的水和有效物质进行反应。同时,过渡区中的上升阶段主要出现在小孔和中孔中,因此,EF段主要出现在中小孔中,即孔径D<8 nm和15 nm≤D≤21 nm的区域中。